Uponor, a global leader in plastics-based infrastructure systems, was preparing to launch an innovative product and required robust field testing to validate its design. The new underground modular system necessitated in-field deflection measurements under varying backfill and load conditions. To meet these demands, Uponor sought experts who could not only ensure precise data capture but also engineer a custom scanning solution that exceeded conventional standards. Our team was engaged to address the following critical challenges:
- A scan operator could not be present within the modular unit during testing.
- Each 3D scan had to maintain consistent coordinates for comparative analysis.
- Real-time deflection feedback was essential at every stage of loading.
Process
Prior to deploying the laser scanning team, several key methodologies were established to ensure a successful outcome. The modular system was to be buried with backfill compacted in stages, and a baseline scan had to be conducted prior to loading. The principal challenge lay in aligning all subsequent scans to the baseline. Typically, this process involves the use of specialized targets as fixed reference points; however, placing these targets within the modular unit was impractical due to potential movement caused by compaction and deflection during testing.
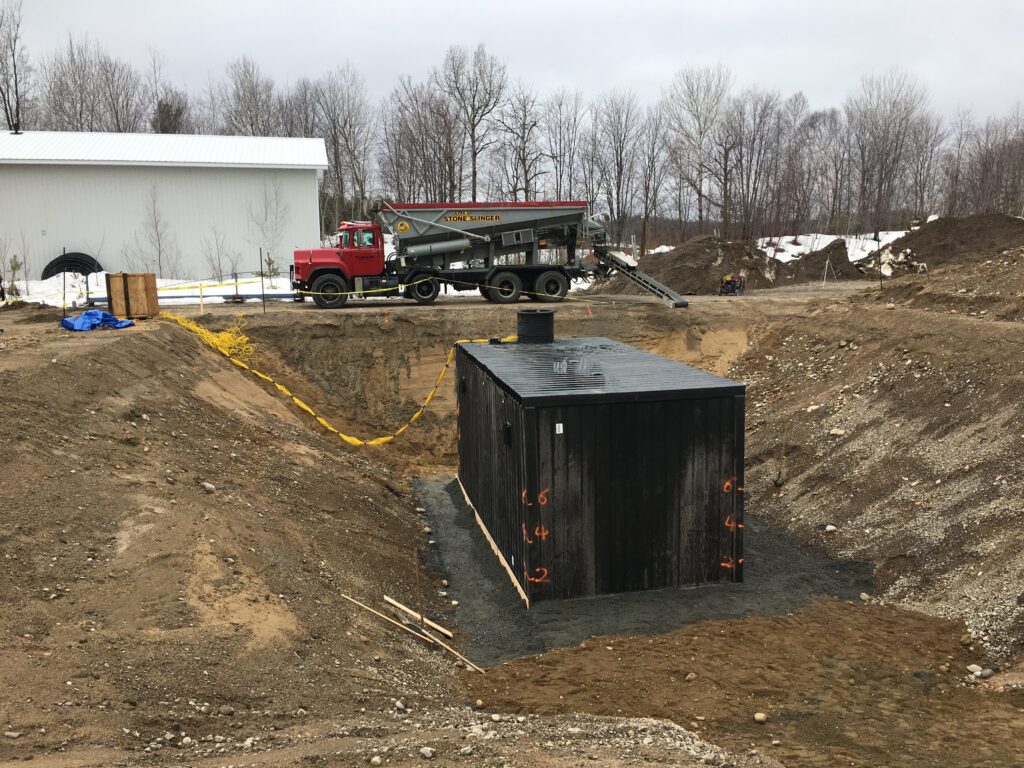
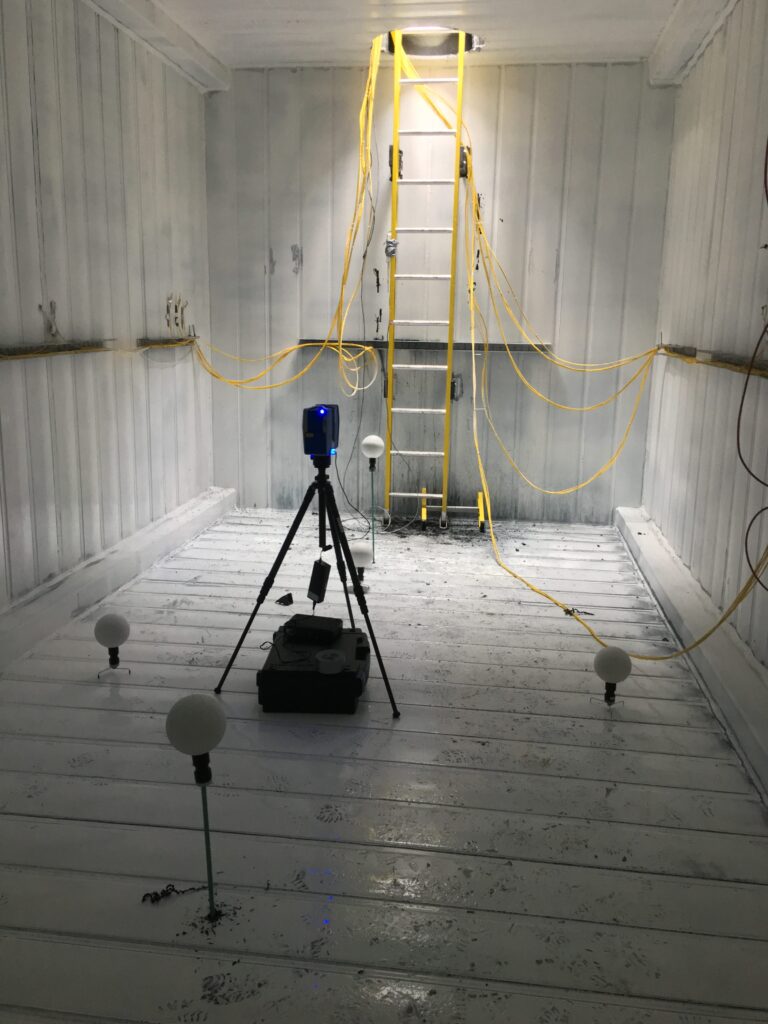
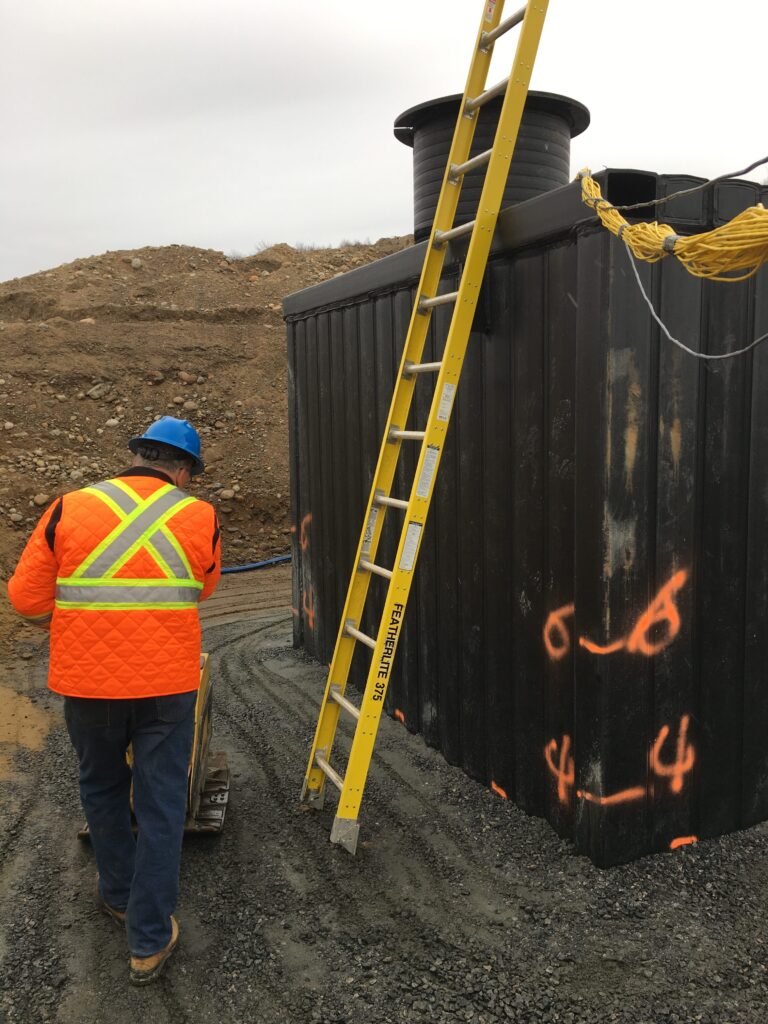
To overcome this limitation, the team collaborated closely with Uponor engineers, examining the base compaction specifications and the anticipated behavior of the modular system under load. They devised a solution involving the placement of 1” diameter bores in three strategic locations at the base of the modular unit. These bores allowed for the secure mounting of stationary reference targets. Large rebar sections were driven into the ground with minimal clearance from the modular unit, and spherical targets were magnetically attached to the top of each rebar section. This ensured that the targets remained unaffected by the modular unit’s movement, enabling all scans to be precisely aligned to common coordinates for accurate comparative analysis.
Another significant challenge was the inability to directly operate the scanner within the buried modular unit. While most modern scanners feature Wi-Fi capabilities, the underground location and 3-foot manhole rendered typical Wi-Fi solutions ineffective. The team resolved this issue by deploying a proprietary Wi-Fi system capable of controlling the scanner remotely from over a mile away, even without direct line of sight.
The final obstacle was providing near real-time deflection analysis. Uponor’s engineers required immediate confirmation that the modular unit’s deflection remained within design parameters before proceeding to subsequent testing stages. A laser scanning specialist remotely extracted and analyzed scan data in the field, delivering preliminary results within one hour of scan completion. This rapid reporting ensured that testing could progress without delay.
Outcome
Over the course of one week, our team successfully captured data across all required load conditions. Leveraging the stationary targeting system, the team generated a layered 3D point cloud for Uponor’s engineering team. Each layer was aligned to the control scan, facilitating seamless analysis. The testing confirmed that the modular unit performed well within expected parameters, validating the design and marking the field tests as a resounding success.